SPIDER
SPIDER: Cable-driven Multiaxial Cursor Machine
Humphrey Yang, Chia Ching Yen
Role: Hardware Design, Firmware and Software Development
This machine is designed to be lightweight and can cover a large area. We designed the system and components as parametric models, meaning that the part models will automatically change shape in response to different machine parameters. A bespoke firmware was developed to control the machine.
Introduction
SPIDER is a scalable cable-mounted cursor machine. Compared to conventional rigid-framed gantry systems, scaling up this design will only cause the weight to increase quadratically (versus cubically), promoting scalability.
Scalable
Polygonal
Parametric Design
3D Models of parts are automatically generated when altering machine parameters and component dimensions
Left: Vertex Unit Design
Left: Cursor Unit Design
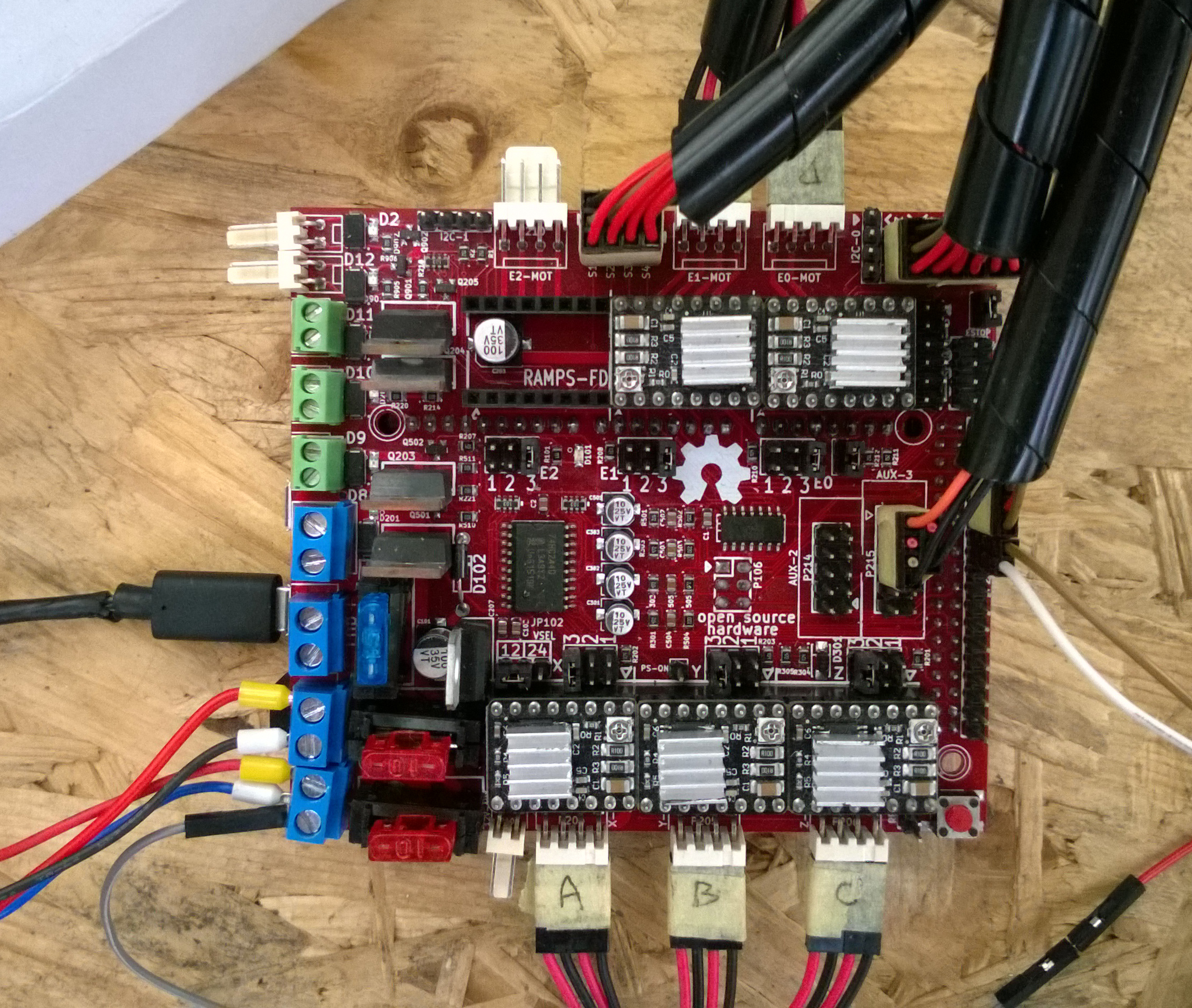

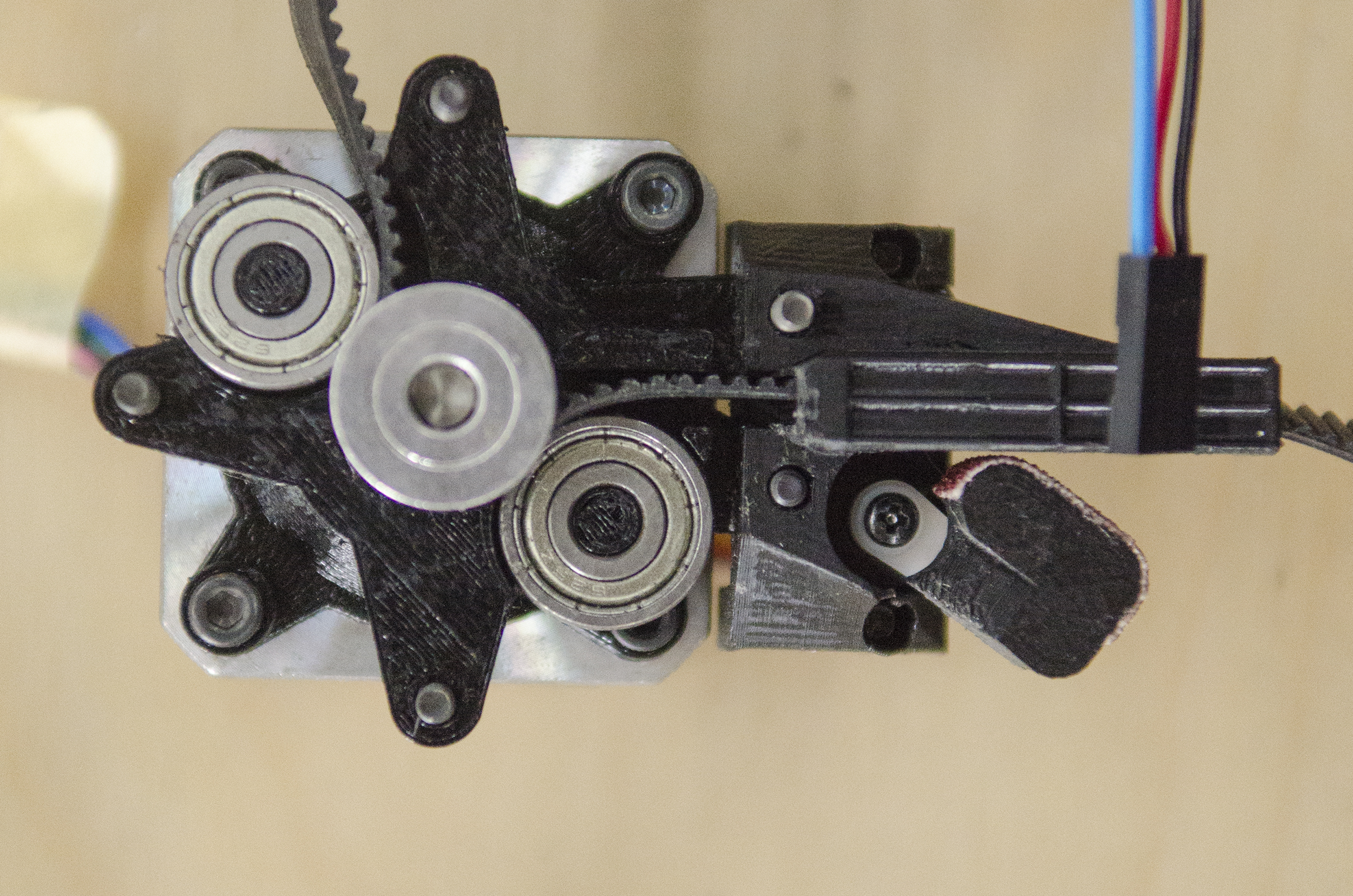



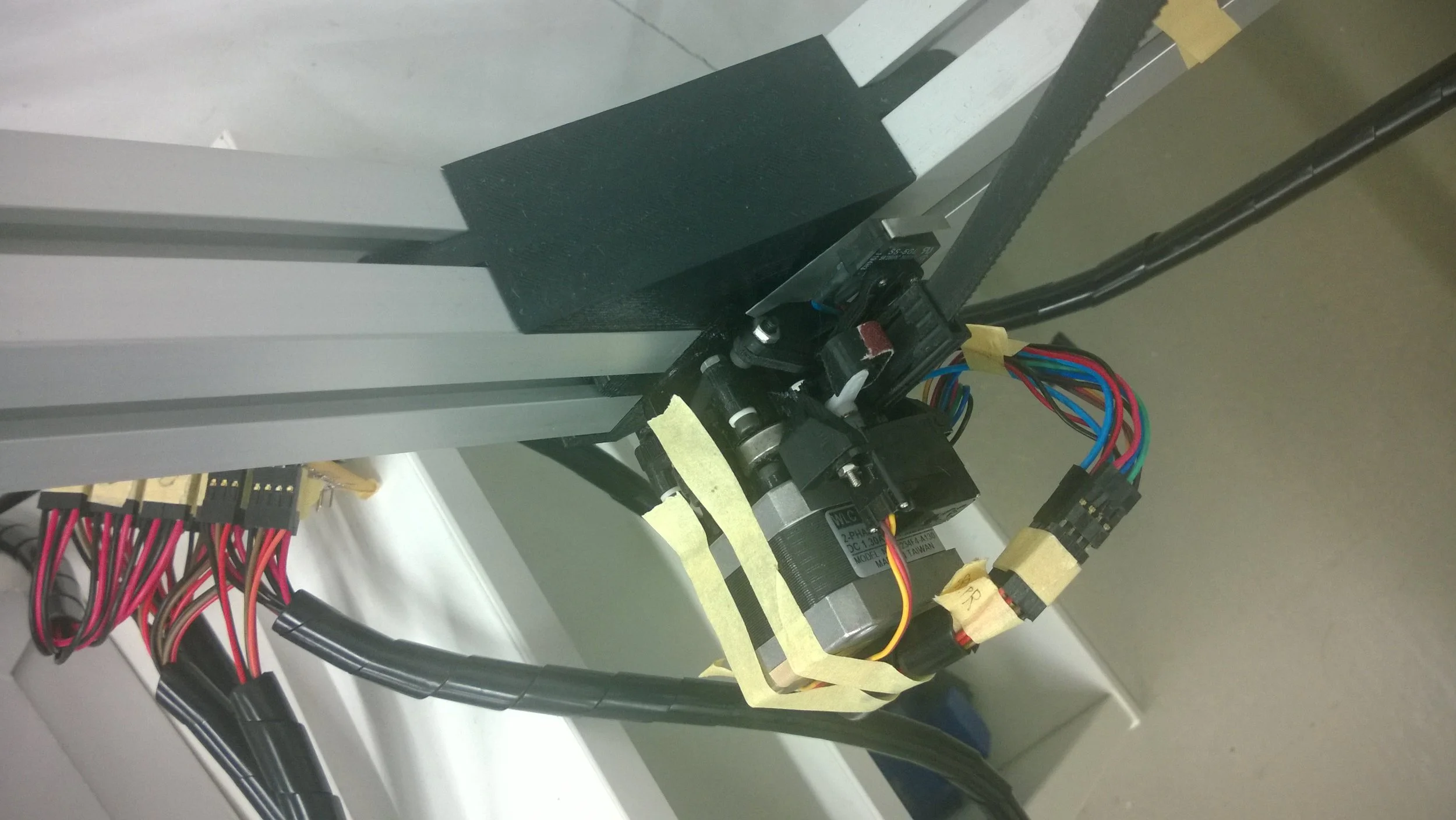
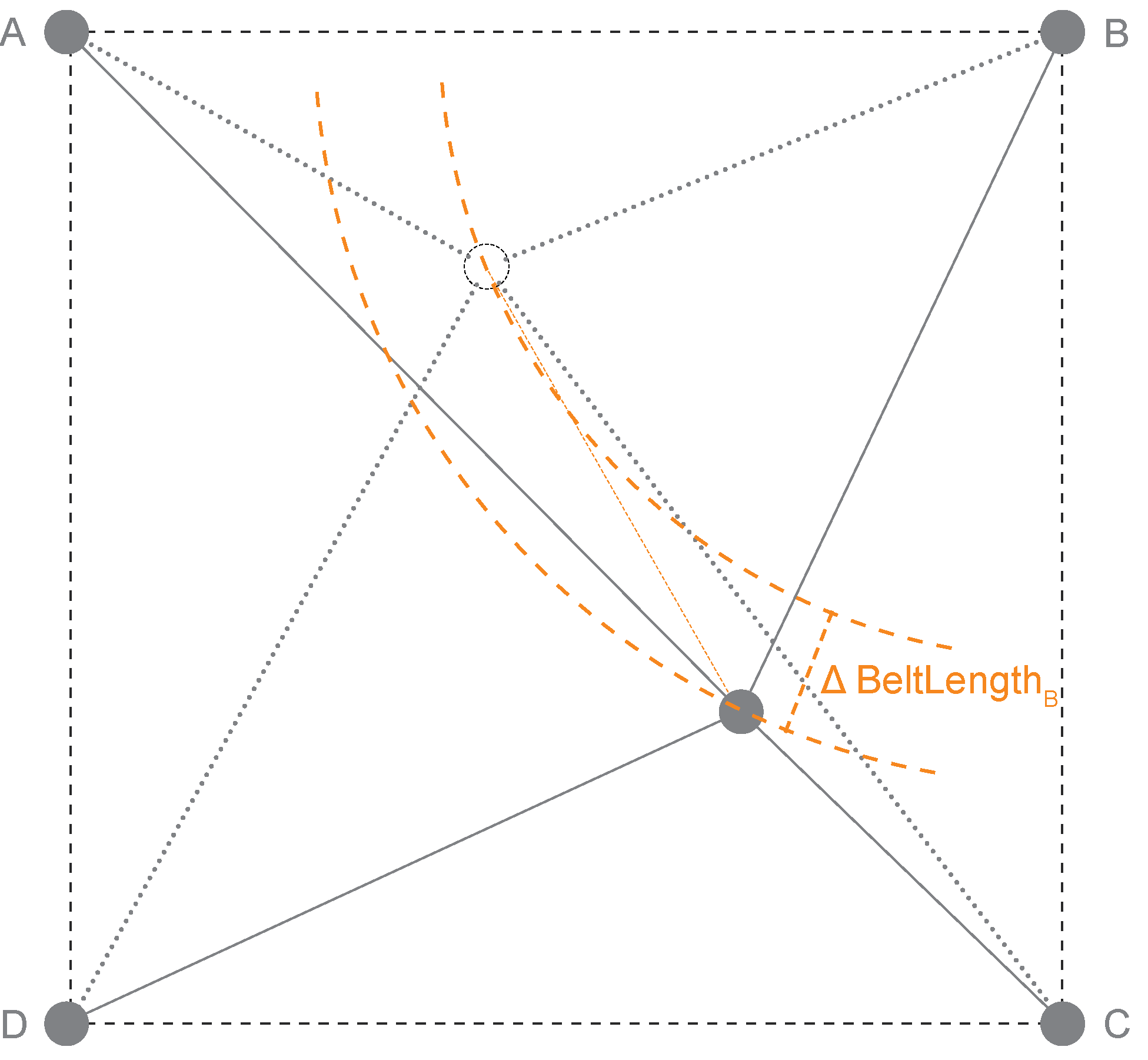

G-Code Compatibility
We use an Arduino Due board to control the movement of the machine. The firmware recognizes G-Code as commands, therefore is easy for designers and makers to use.
To complete a movement, the system first computes the corresponding belt length deviation at each vertex, then set individual tick intervals for the motors to achieve a synchronized movement.
The belts lengths change nonlinearly in response to cursor movements. In this video, the belts are slacking due to falsely (linearly) interpolating belt lengths. Later revisions bypass this problem by segmenting the movement into smaller segments, in which the lengths change almost linearly.