Composite 4D Printing
Material Characterization and Precise Finite Element Analysis of Fiber Reinforced Thermoplastic Composites for 4D Printing
Yuxuan Yu*, Haolin Liu*, Kuanren Qian, Humphrey Yang, Matthew McGehee, Jianzhe Gu, Danli Luo, Lining Yao, Yongjie Jessica Zhang (* Contributed Equally)
This is a collaborative effort between the Morphing Matter Lab and the Computational Bio-Modeling Lab at CMU
Publication: Material characterization and precise finite element analysis of fiber-reinforced thermoplastic composites for 4D printing (Journal of Computer-Aided Design 2020) PDF
Role: Computational and fabrication toolmaking, application design, dataset generation, documentation
This paper propounds a composite structure design made of two materials - polylactic acid (PLA) and carbon fiber reinforced PLA (CFPLA) - to increase the structural strength of 4D printed artifacts and a workflow composed of several physical experiments and a series of dynamic mechanical analyses (DMA) to characterize materials. We apply this workflow to 3D printed samples fabricated with different printed parameters to accurately characterize the materials and implement a sequential finite element analysis (FEA) to achieve accurate simulations.



We used dynamic mechanical analysis to characterize both PLA and CFPLA to create material models, which were then used to develop a finite element analysis pipeline to simulate their deformations.

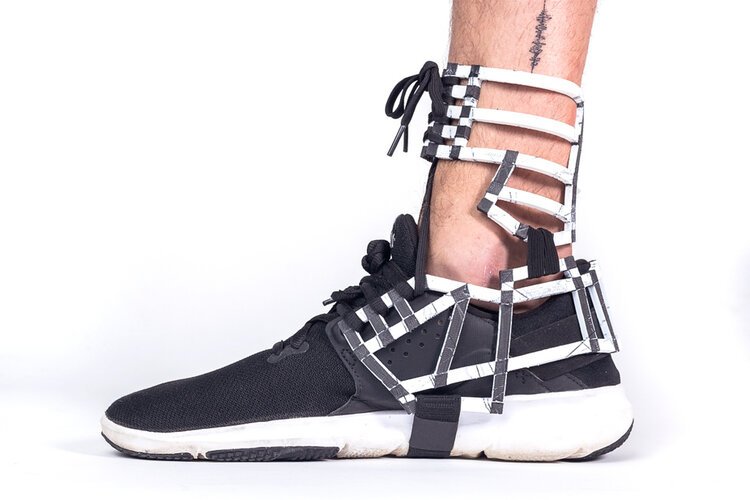

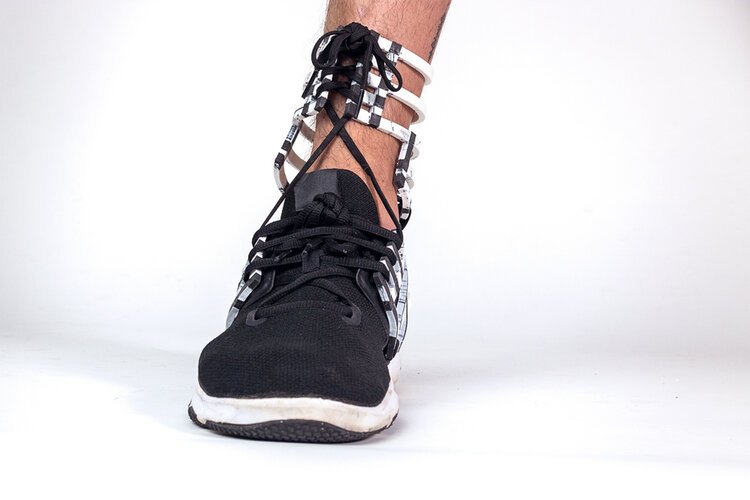
Introducing CFPLA into 4D printing allows us to create structurally functional objects, such as an ankle support, with reduced printing time, extending 4D printing’s application space.
Acknowledgment
This project was mainly supported by the Carnegie Mellon University, United States Manufacturing Futures Initiative (MFI) made possible by the Richard King Mellon Foundation, United States, and a Honda grant. We are also especially thankful to Mr. William Pingitore, who supervised us conducting the four-point bending experiment, and Dr. Guanyun Wang, who helped us on multiple design applications, and Prof. Christopher Bettinger in the Departments of Materials Science and Engineering and Biomedical Engineering, who provided the DMA facility. The authors acknowledge the use of the Materials Characterization Facility at Carnegie Mellon University, United States supported by the grant MCF-677785.